6月に入りました。
関東は未だ梅雨入りせず。
今年は猛暑になると言われていますが、果たしてどーなるか…
毎年温暖化が続くとなると、服作りの内容も変わってきます。
数年後にはもう夏服メインになるのではないかと心配になりますが、、
四季がある日本は有数のファッション都市。
何年先も日本の季節を楽しみたいところですね〜。
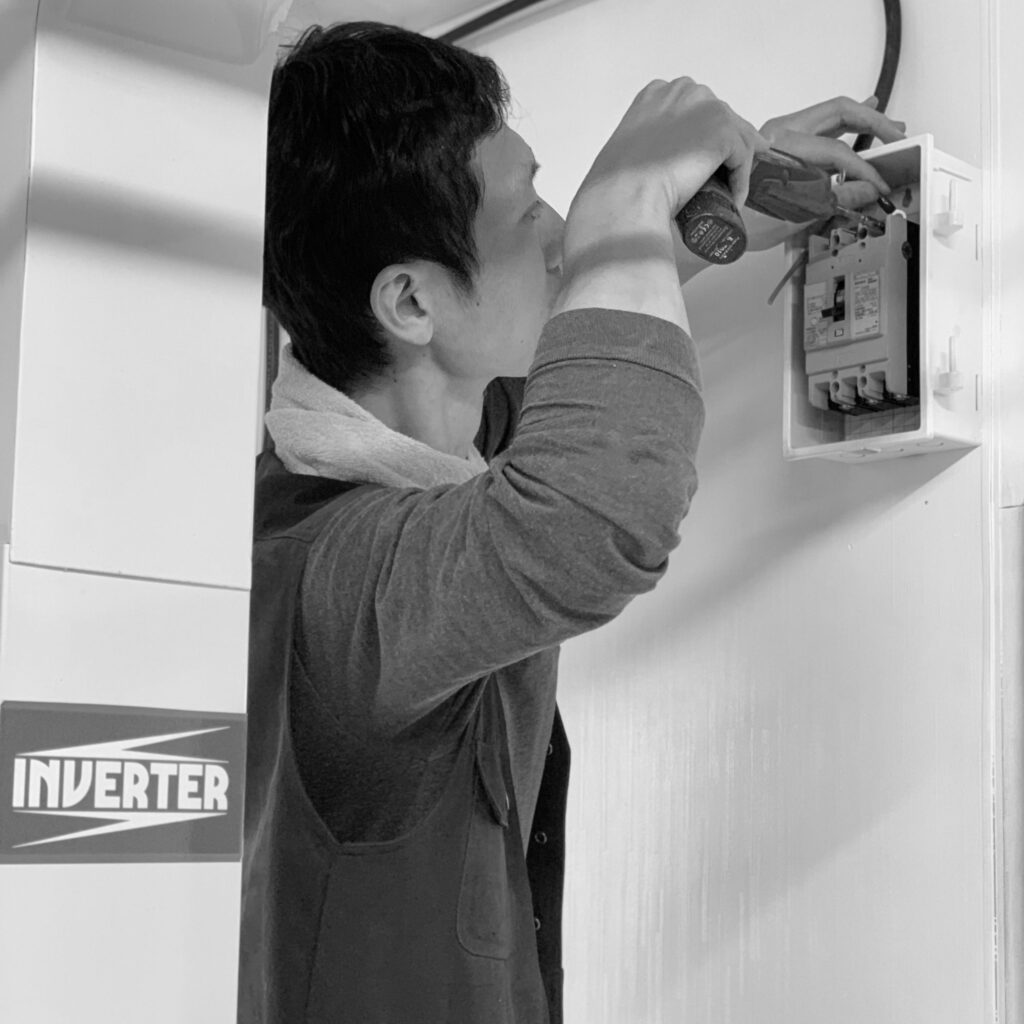
そして新作業場の改装も最終仕上げ段階へ。
地元ファミリーの電気マスターと共に動力設備工事を決行。
これでようやく三相200Vを使用できるので、お隣のバキュームアイロン台が遂に稼働する、ハズ。
壊れてなければ。笑
その他200Vの工業用ミシンもバンバン導入できるってワケです。これで怖いもの無し。
てなわけで、
ぼちぼち本題へ。笑
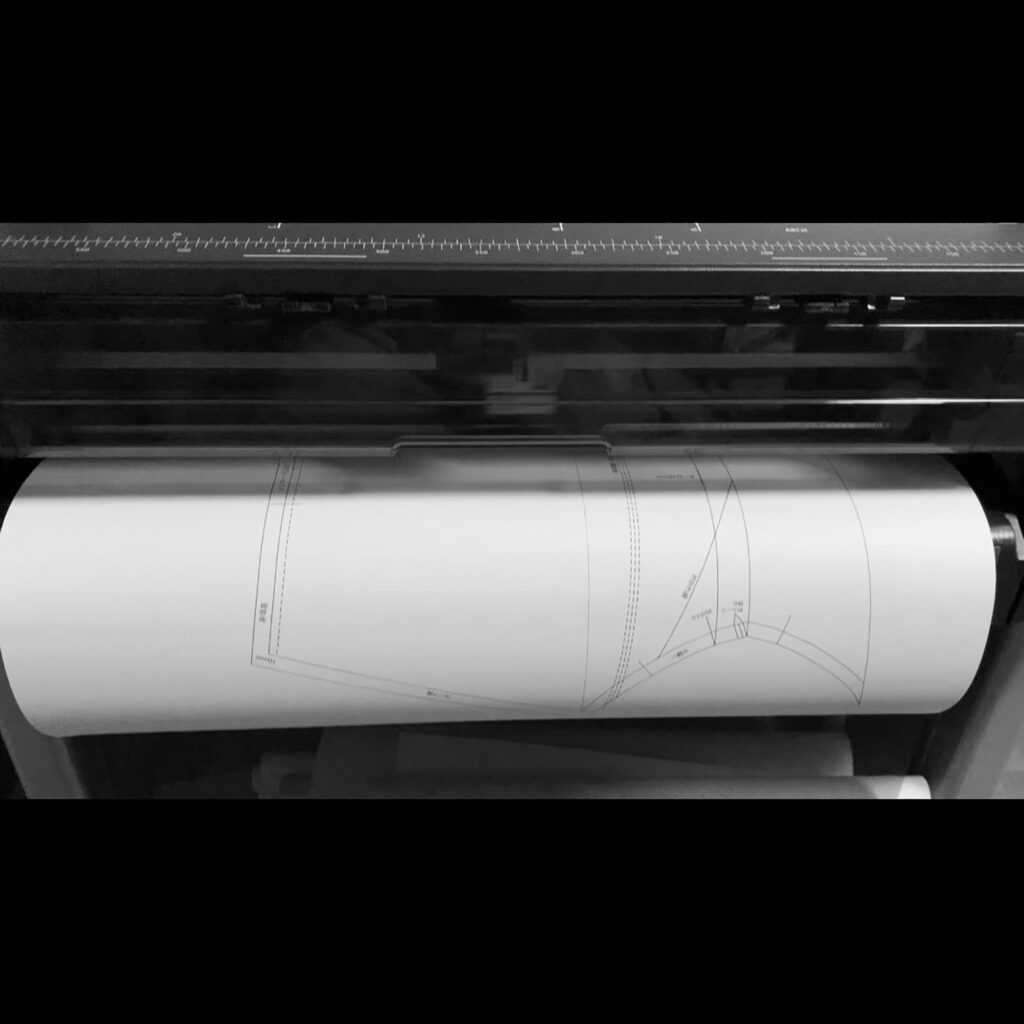
機会があったのでたまには縫製工程のお話でも。
まずはPCでパターンを作成ですね。その後は印刷機に出力。
これも大判プリンターが無いとかなりシンドい作業となります。
プリンターがない昔は紙をつなぎ合わせて型紙作ってたなぁ〜…そんな苦い思い出。笑
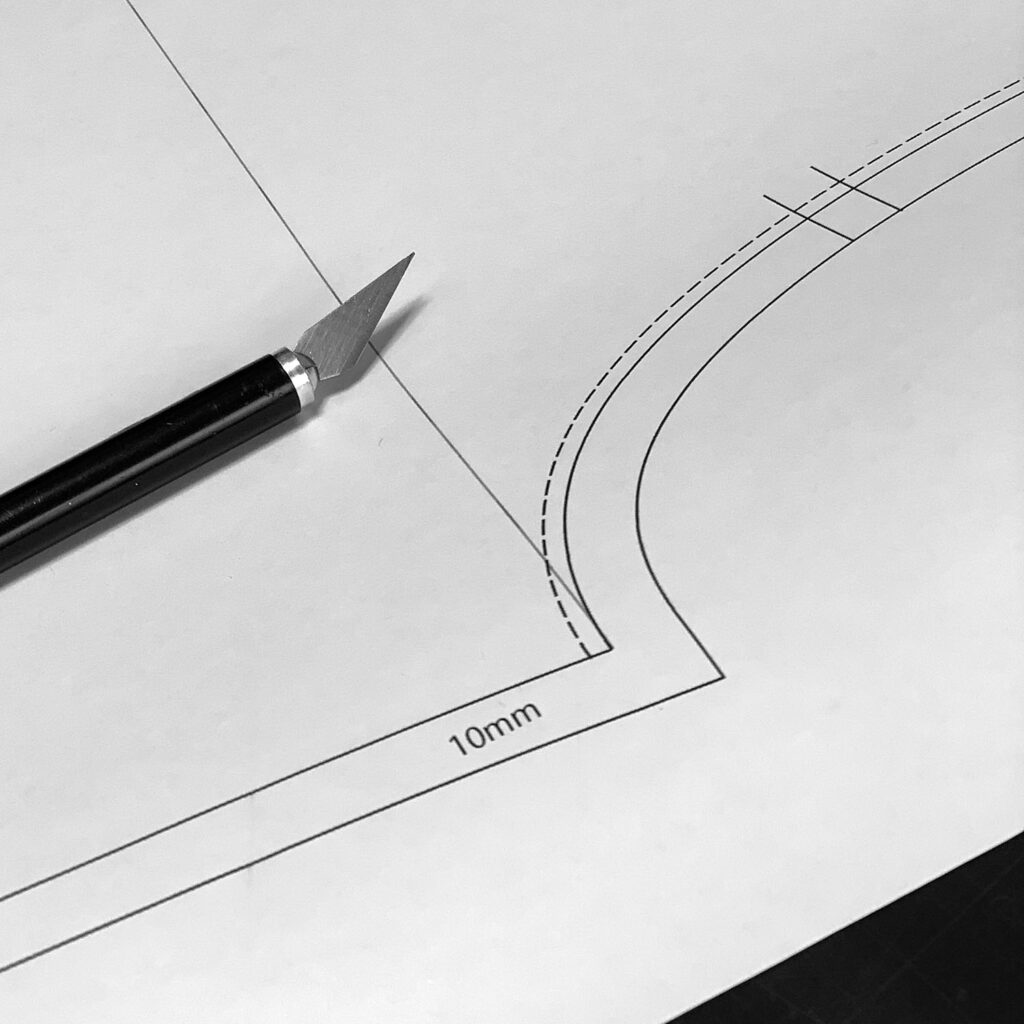
出力を終えたらパターンをカット。
本当はプロッターカッター付きの印刷機があれば速攻で終わるんですが、毎日使うもんでないんでこの辺は時間かかりますが手作業でカット。
ただ手作業でカットする自分なりのメリットは、パターンの間違いを発見できることですかね。
細かい箇所までパターンには記載するので、時たま漏れがあったりもするので。
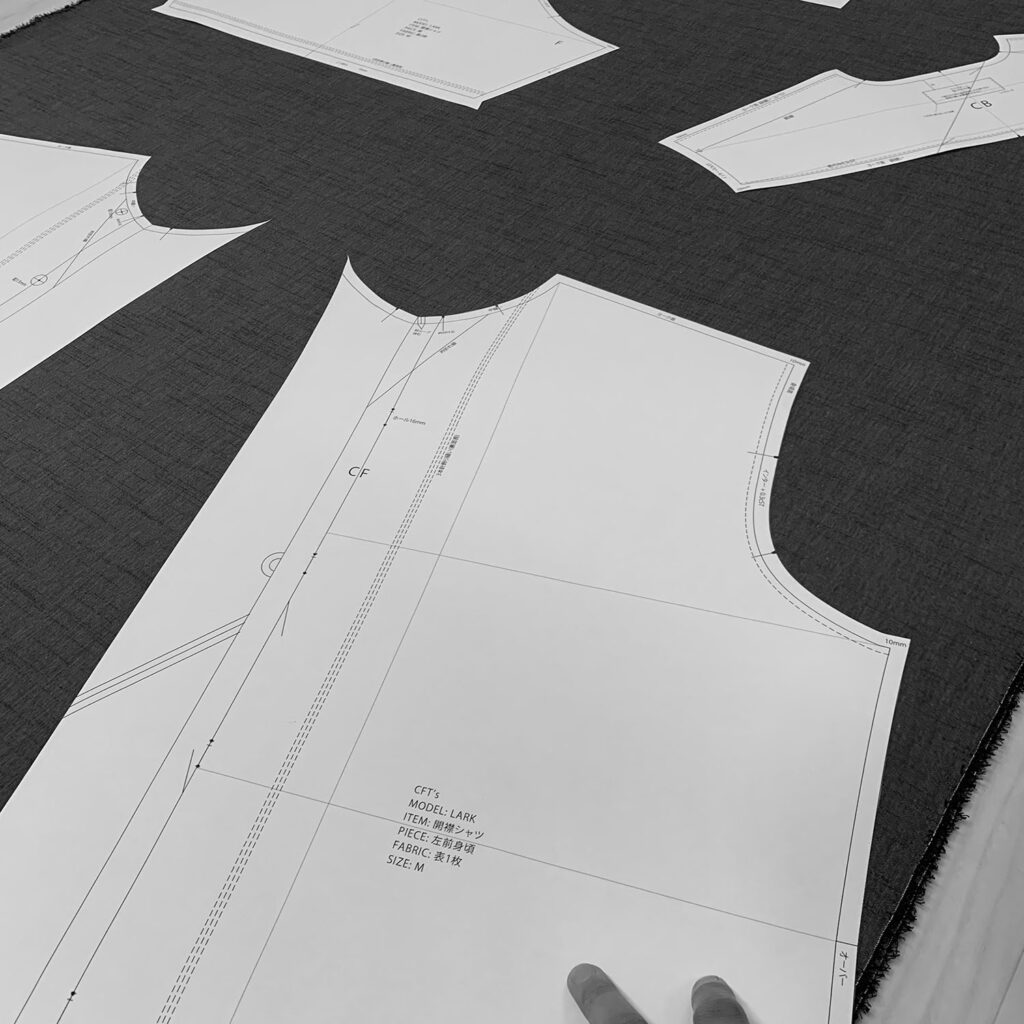
続いて延反作業を終え、裁断するパターンを配置。
PCである程度用尺計算し、配置のイメージも決めておきます。
それに合わせ配置していくのですが、生地の巻数に『乱』がある場合は意外に生地を多くも少なくも取れる場合があったりするので、その辺は現場合わせ的な感じです。
パターンの配置も生地の向きをどのように使うか。ここは生地の特徴を理解したデザイナーの判断って感じですかね。
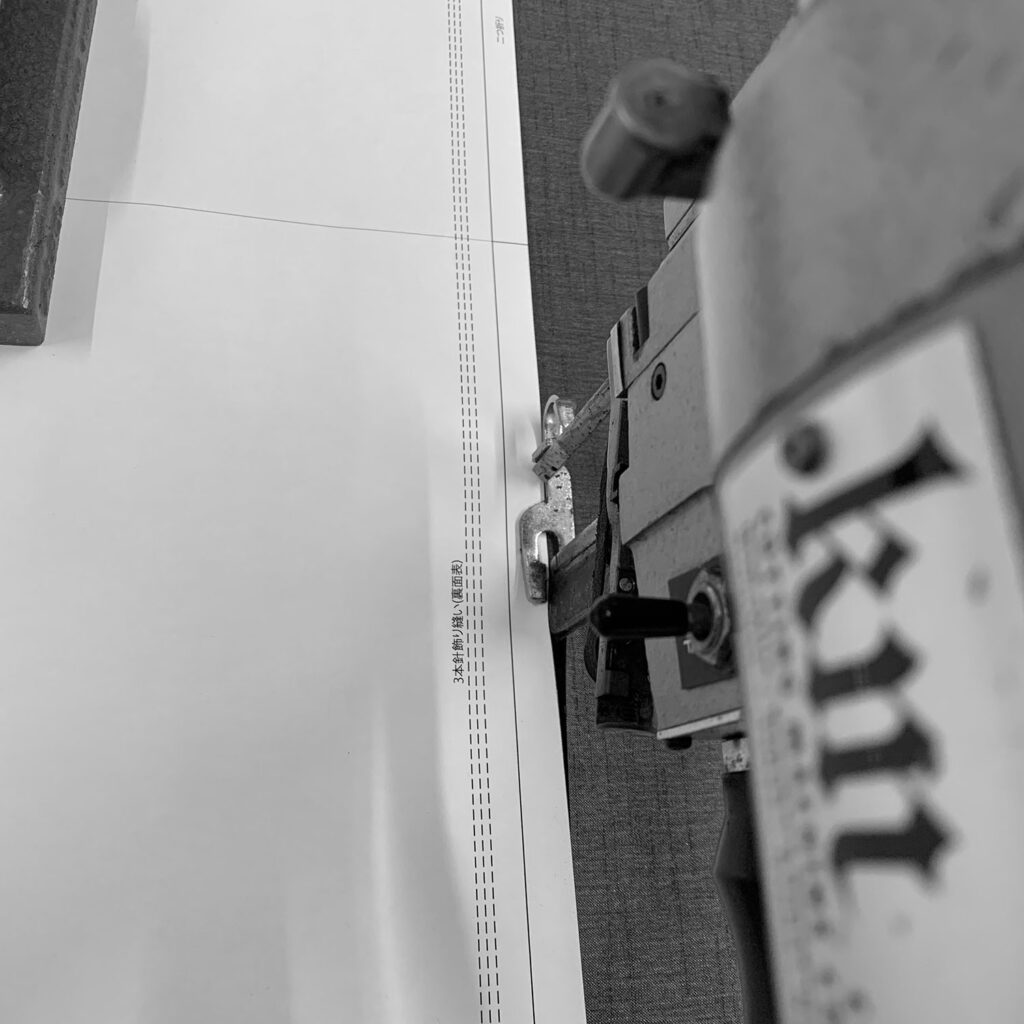
続いて裁断。ここは最重要工程かつ最腰痛ポイント。腰バンドを巻いていざ。
裁断機を使用して何枚も重ねた生地を一括裁断。緊張する作業です。
新しいものでは自動裁断機という優れものがありますね。
DXF等に書き出したデータで自動で裁断してくれる何とも頼もしい超大型機械です。
これを導入するのはムリ。場所もコストもムリ。もし裁断が不安な場合は外注依頼するのがベストですな。
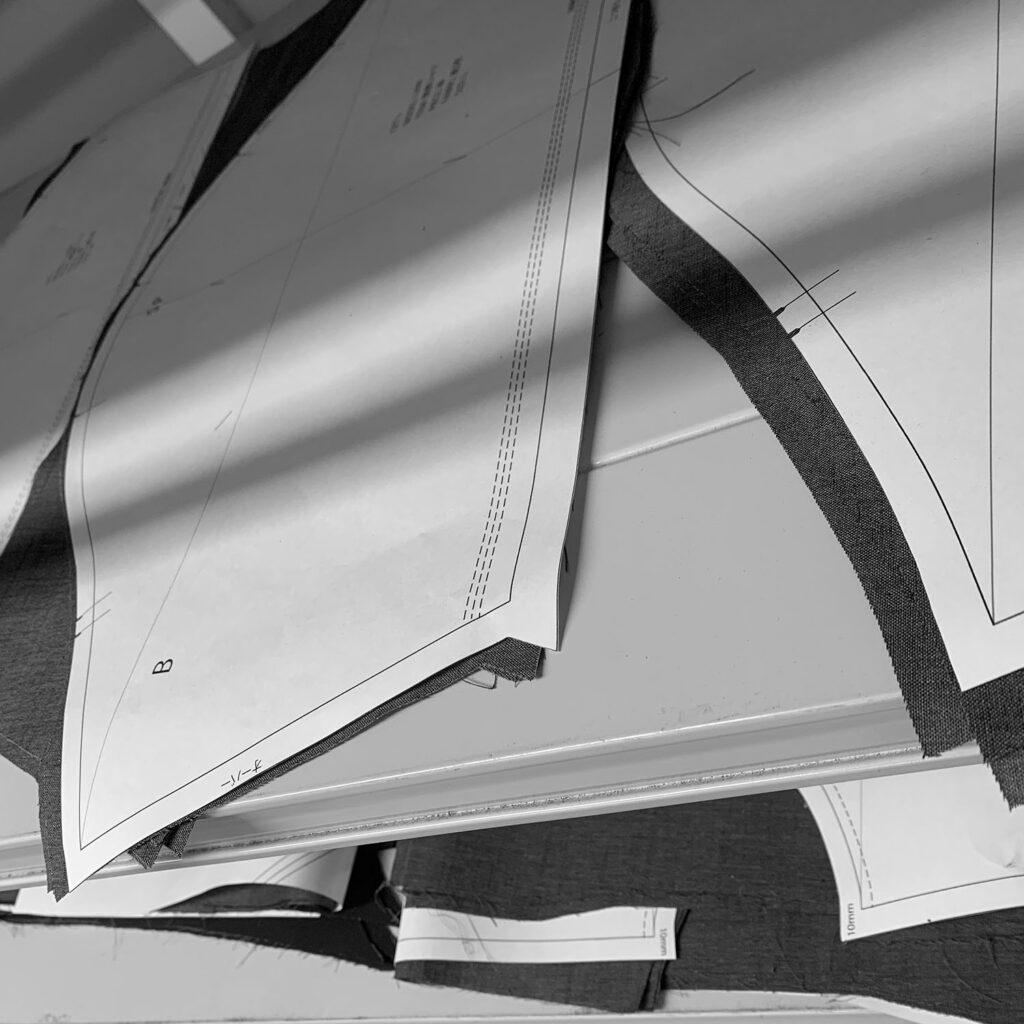
ひとまず一反まるっとパーツごとに切り出し。
アイテムごとに用尺が変わるのに加え、オーバーサイズになればなるほど数量が取れません。
アイテムのパーツ数、カラー展開、生地の在庫量、生地の巾(シングルorダブル)等、
色々と頭を悩ませ計算しながら製作していくのです。
ここまで終えたら次からは組み立て縫製にシフトチェンジ。
という訳で、
一般的に量産工程①はザックリですがこんな感じですかね。
洋服を作るという工程は一般的にあまり知られていないんじゃないか?
と思い、珍しく内容を書いてみました。
まぁ知らないといけない訳ではないんですがね。何となく。笑
業界には既存のアイテムにプリントや刺繍の二次加工のみというやり方もありますが、
CFT’sではイチからパターン作って生地選んで縫製して作ったアイテムとなります。
仮に既存ボディを使う際は公表いたしますので。笑
服を作るという工程は簡単なことでは無い!というお話でした。
ちゃんちゃん。